LOST-WAX CASTING
Experience in wax carving, lost-wax casting, filigree fabrication, soldering, and finishing. 2023 to present.

“After Amsterdam”
Wax Carving, Casting, Stone Setting
September 2024
Wax Carving, Casting, Stone Setting
September 2024
“Barca”
Wax Carving, Casting, Inlay
September 2024
Wax Carving, Casting, Inlay
September 2024

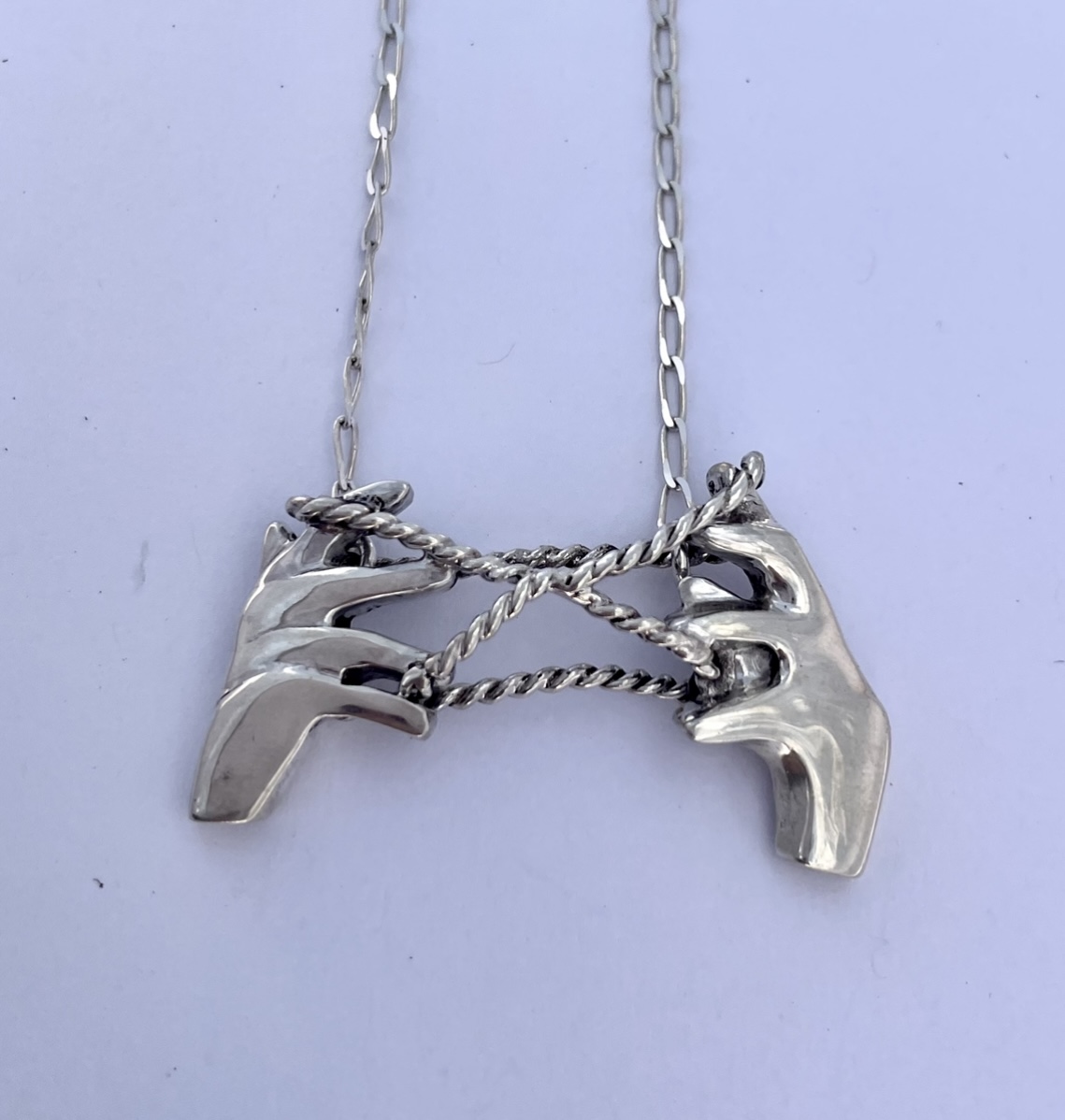
“Human Jaw”
Wax Carving & Casting
September 2023
Wax Carving & Casting
September 2023
“A Cat’s Cradle”
Carving, Casting, & Soldering
September 2023
Carving, Casting, & Soldering
September 2023


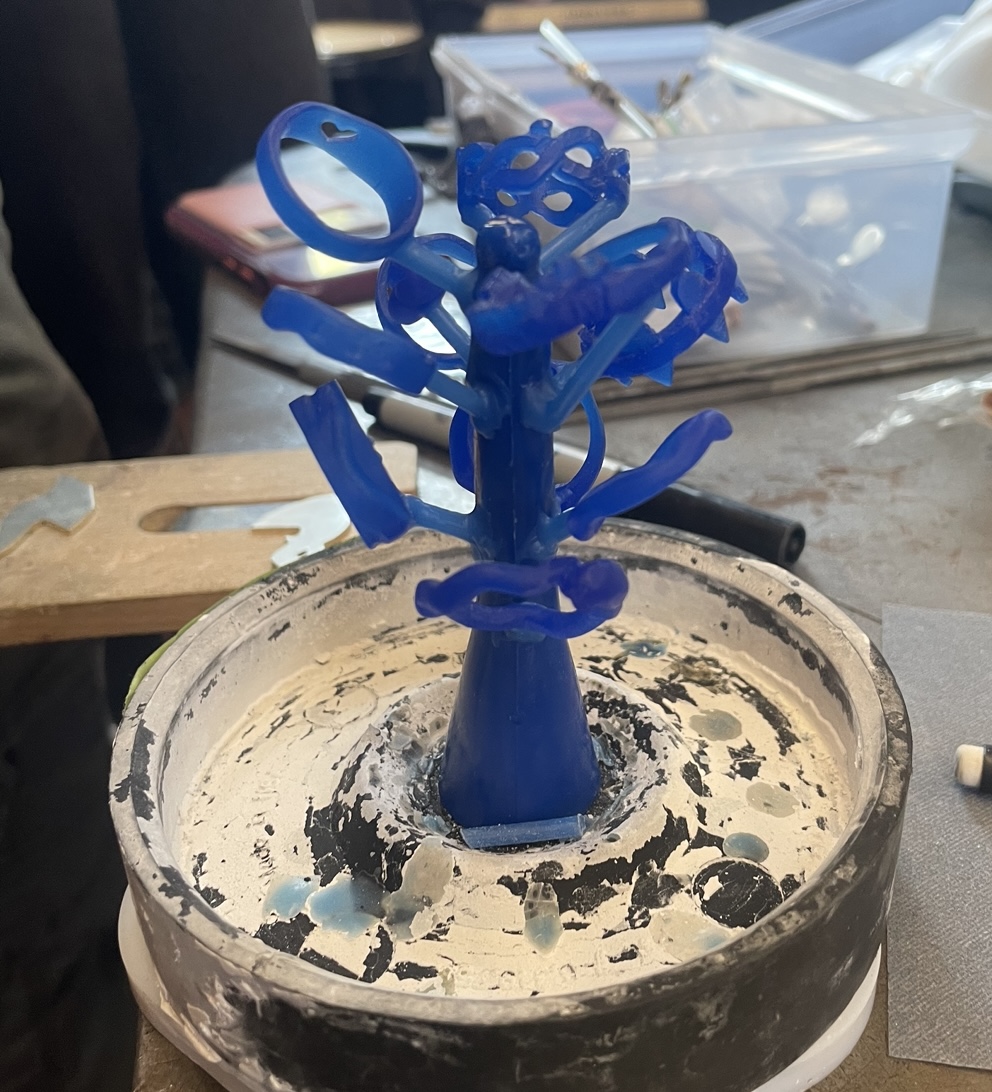
Wax Carving & Casting
For lost wax carving the first step is to hand carve the design. After reaming the cylindrical wax to my ring size, we can get to carving. Using anatomical diagrams from various angles, I illustrated each side of the jaw and traced onto the wax for reference. Then, using a mix of drill bits and burrs on the dremel, small round and flat files, and intricate carving tools, I turned my 2D drawing into a 3D sculpture for each ring. These are added onto a tree for the casting process, invested, and finally cast.
For lost wax carving the first step is to hand carve the design. After reaming the cylindrical wax to my ring size, we can get to carving. Using anatomical diagrams from various angles, I illustrated each side of the jaw and traced onto the wax for reference. Then, using a mix of drill bits and burrs on the dremel, small round and flat files, and intricate carving tools, I turned my 2D drawing into a 3D sculpture for each ring. These are added onto a tree for the casting process, invested, and finally cast.

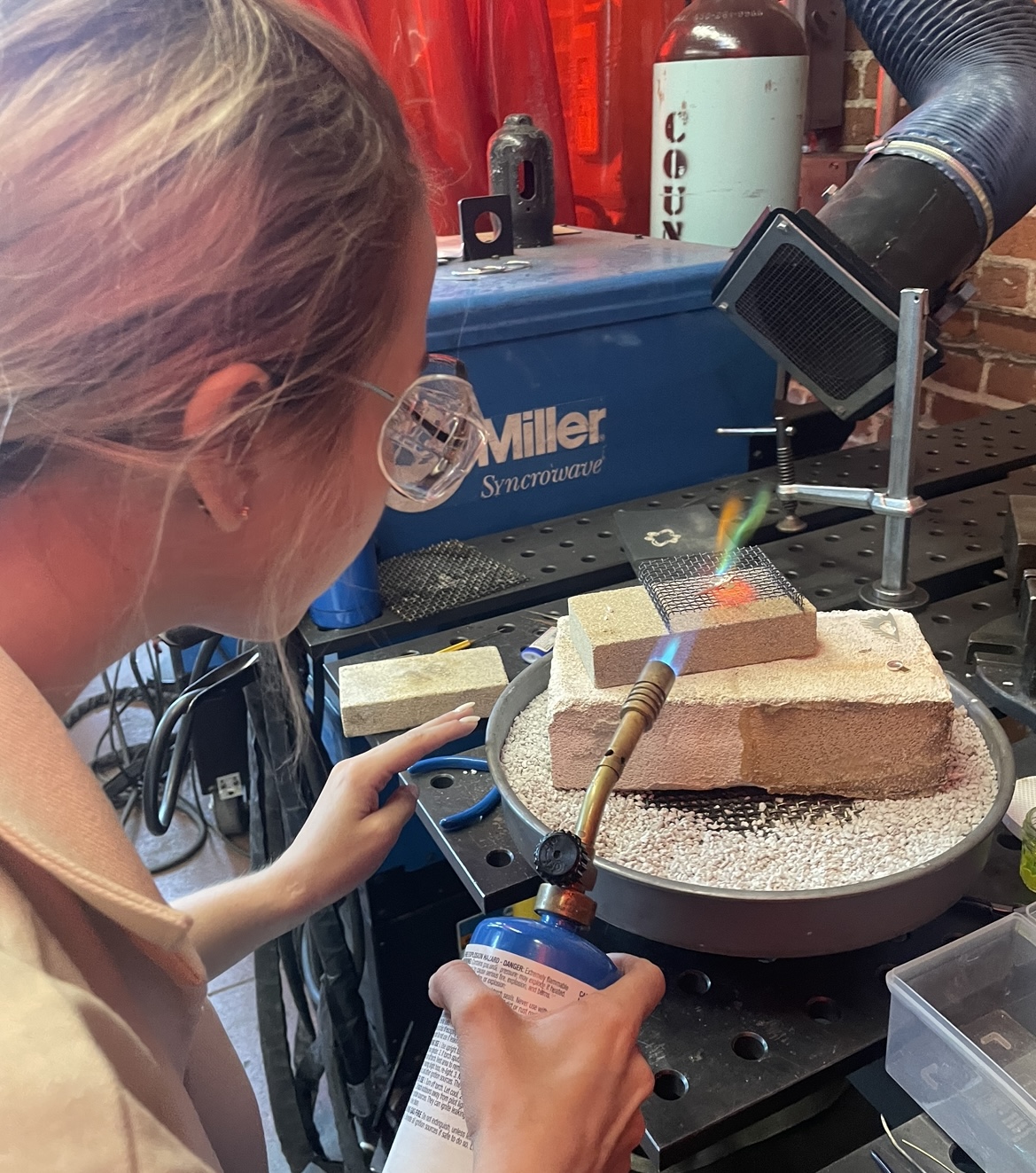
Soldering
To meld pieces of silver together, like in “A Cat’s Cradle” I used various soldering techniques. I wanted the filigree I made to be truly integrated into the work, rather than just decoration- so I made a rope design out of it, shaped onto my casted pieces, and cut to size. To get the rope to stay on the back, I drilled holes the same circumference as the wire and soldered the top and bottom horizontal ropes in using bits of hard solder in the divets. Once secured, I tried a different technique for the overlapping diagonal ropes. After placing properly, I heated the entire piece, using a long piece of easy level solder to dab where I wanted to attach the pieces. In this case, I melted the bottom left wire- which meant adding a new piece of filigree in it’s place, and repeating the process. It turned out to be a happy accident, and the replacement wire really made the rope look as if it were twisting around each other. After soldering, all the pieces go into the pickle to process before moving onto finishing.
To meld pieces of silver together, like in “A Cat’s Cradle” I used various soldering techniques. I wanted the filigree I made to be truly integrated into the work, rather than just decoration- so I made a rope design out of it, shaped onto my casted pieces, and cut to size. To get the rope to stay on the back, I drilled holes the same circumference as the wire and soldered the top and bottom horizontal ropes in using bits of hard solder in the divets. Once secured, I tried a different technique for the overlapping diagonal ropes. After placing properly, I heated the entire piece, using a long piece of easy level solder to dab where I wanted to attach the pieces. In this case, I melted the bottom left wire- which meant adding a new piece of filigree in it’s place, and repeating the process. It turned out to be a happy accident, and the replacement wire really made the rope look as if it were twisting around each other. After soldering, all the pieces go into the pickle to process before moving onto finishing.
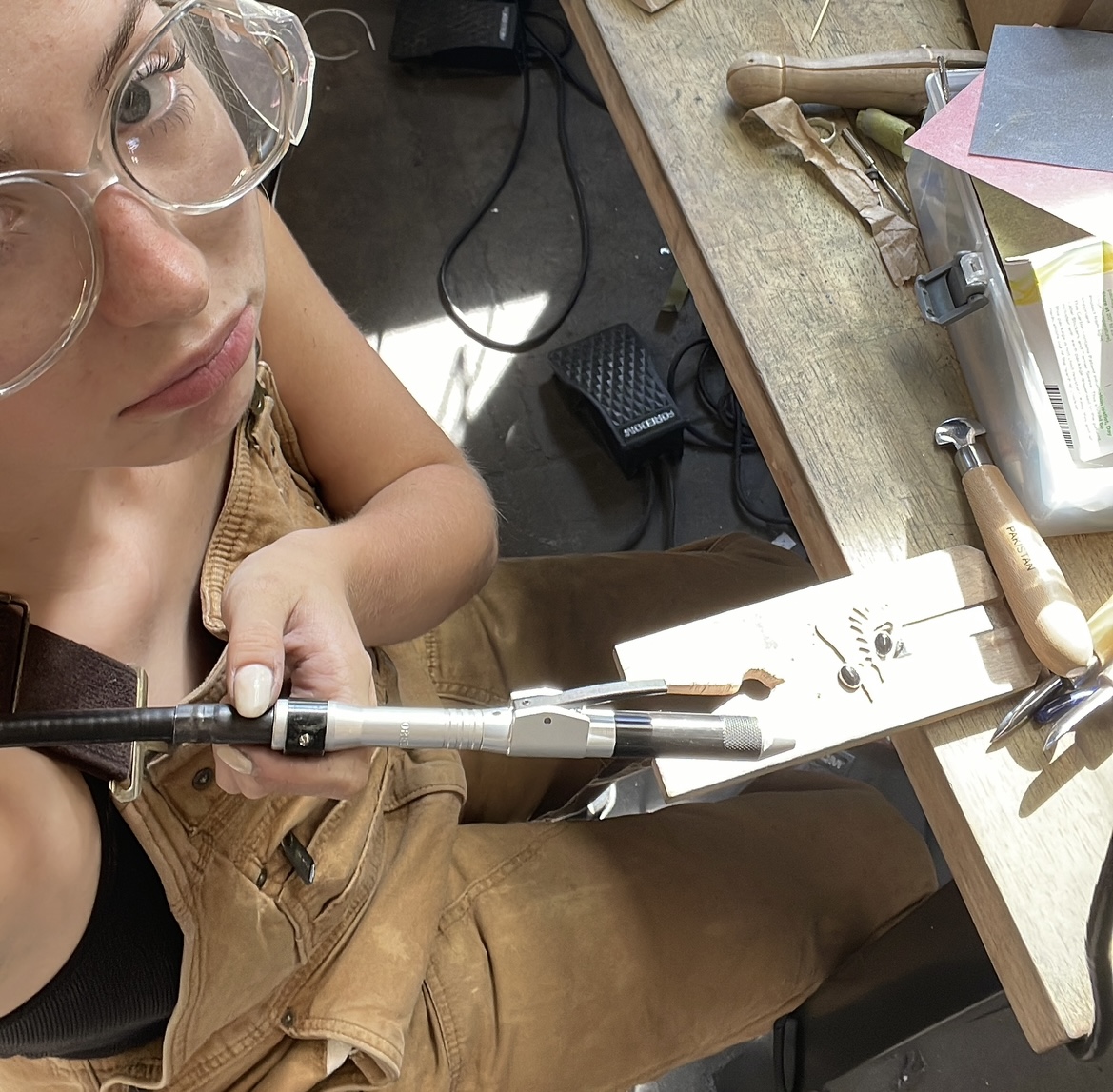
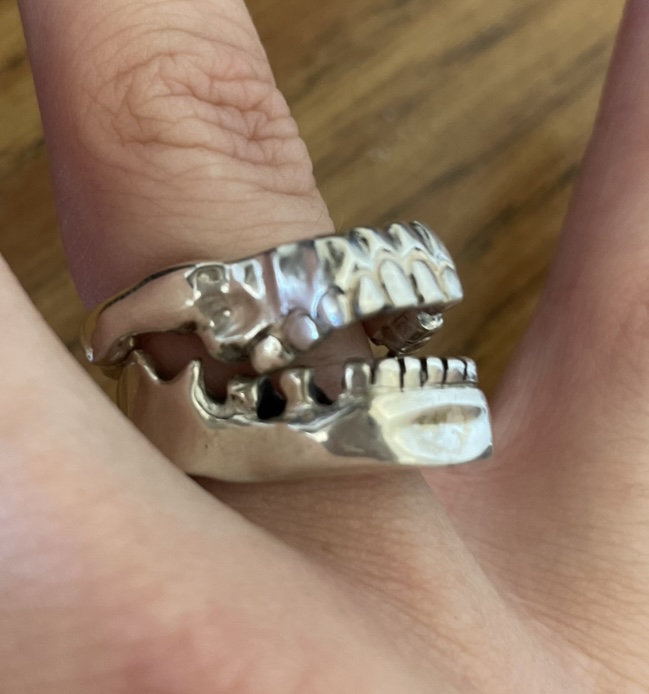
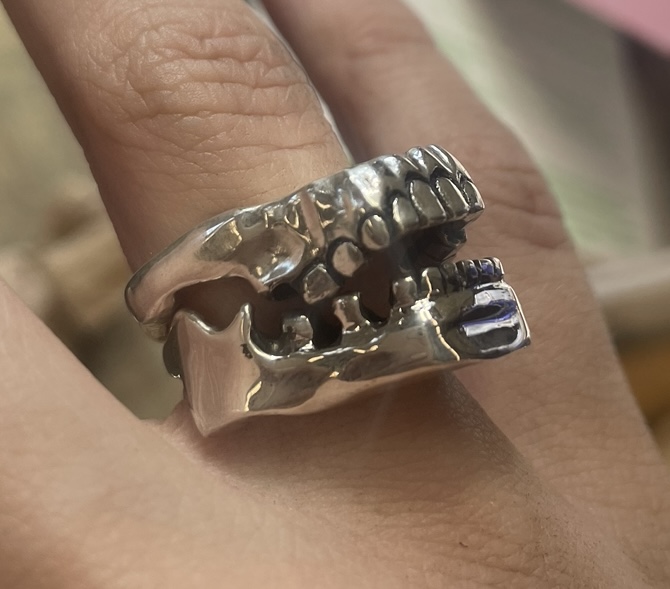
Finishing
Finishing is different for every project. Foremost is filing out any big imperfections, then sanding until completely smooth. Then, polishing. For “Human Jaw,” I used polishing compound and a variety of machines to get in every crevice, then added to warm water and scrubbed to remove any black spots from the process. For this piece, I used oxidizing chemicals to blacken between the teeth and gums. If bezel setting, adding the stone. And if making a pendant or earrings, we also add on jumprings, chain, and closures for a truly finished, wearable piece of jewelry.
Finishing is different for every project. Foremost is filing out any big imperfections, then sanding until completely smooth. Then, polishing. For “Human Jaw,” I used polishing compound and a variety of machines to get in every crevice, then added to warm water and scrubbed to remove any black spots from the process. For this piece, I used oxidizing chemicals to blacken between the teeth and gums. If bezel setting, adding the stone. And if making a pendant or earrings, we also add on jumprings, chain, and closures for a truly finished, wearable piece of jewelry.